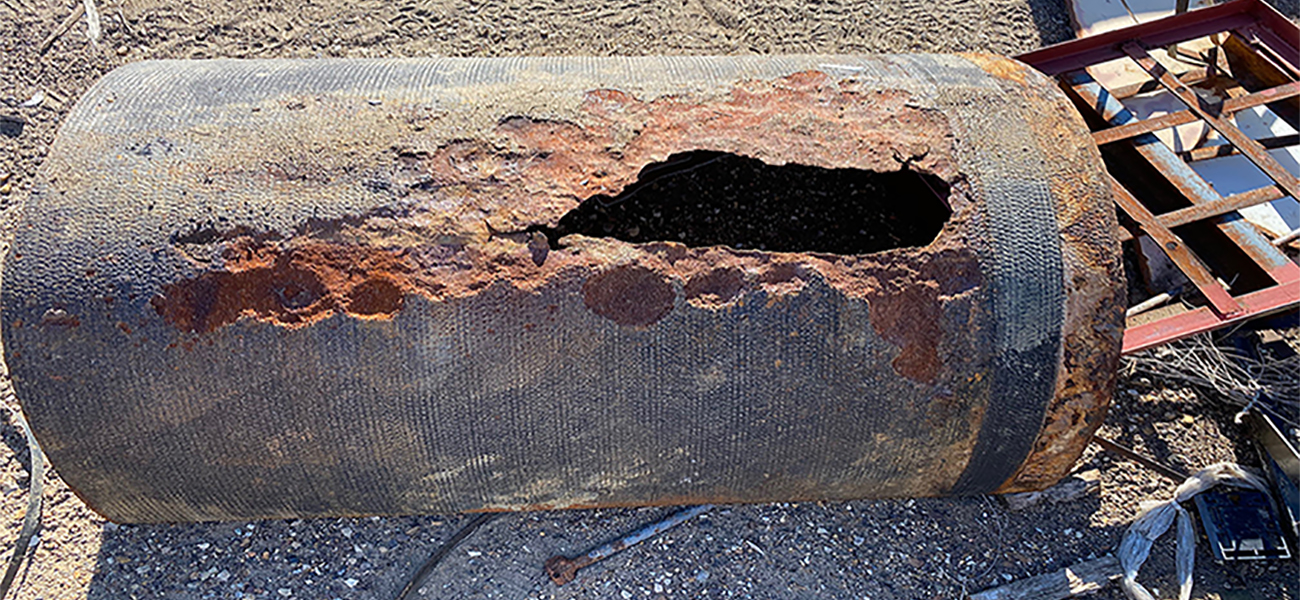
INSIGHT
Pipeline condition assessment technologies for rural and regional water systems
Connect with us
It is an understatement that operating margins are tight for publicly owned water utilities and rural and regional water systems. With all the problems faced on a day-to-day and week-to-week basis by these water systems and their not-for-profit nature there usually is no money to spare for conducting a pre-emptive pipeline condition assessment program.
Leaks on PVC pipeline distribution systems are relatively few and most utilities simply fix leaks as they occur and have grown large enough to surface above ground and be located. Mathematically expressed, the Risk, which is equal to the Cost of Failure multiplied by the Likelihood of Failure, is usually not large enough to justify a special condition assessment investigation. This is especially true for smaller diameter distribution pipelines made of PVC where the cost of leak repair or replacement of a defective section is relatively low and the impact of an outage is minor. There are situations however where a condition assessment program might make sense and a review of the available technologies in this rapidly changing field is worthwhile.
New AWWA Manual
American Water Works Association (AWWA) has a recently published Manual of Water Supply Practices entitled Condition Assessment of Water Mains (M77). This manual covers a broad range of technologies for conducting condition assessments as well as discussions on planning, cost benefit analysis, and desktop condition assessments using available information. All of the technologies discussed in this article are included in M77.
The cost of a leak or defective pipe repair is not just the dollar amount spent by the utility or system to physically replace or repair the pipe. Those direct costs are obvious; other less obvious and indirect costs include those for things such as service interruption, public notice, regulatory costs, water loss, and water damage. These costs can be significant and together with the cost of repair and replacement can make the pipe assessment cost effective. Sometimes it can even just be the potential for these costs that drive the decision.
For example, the system might have a high-value customer such as a health care facility, airport, or industrial user for which an extended outage of more than one day is not tolerable. Distribution systems usually have larger transmission pipelines conveying water to a storage facility or into a service area before branching down into smaller diameter pipelines. For these larger diameter pipelines the impacts and costs of failure both direct and indirect are substantially larger along with the impacts of an outage and a pipeline condition assessment may become more and more cost effective.
A pipeline condition assessment doesn't have to involve a large expense. Office or desktop assessments can include reviewing leak and break history, age, pipe material, pressure classes versus operating pressures, and in the case of metallic pipelines, soil corrosivity, cathodic protection systems, and test data. When choosing the level of assessment to be conducted, the sensible approach is progressive. Start with the less expensive options to gain a general understanding of the pipeline condition and then determine the next steps. Plan for multiple assessment levels as no single method will provide all the information.
GETTING STARTED
In general, there are four variables to consider.
- Degree of inspection: Is the assessment being done to find small defects, leaks, or for finding out the general condition of the pipe?
- The amount of pipeline that will be assessed.
- Access: Can tools easily be inserted and extracted? Can it be taken out of service, and if yes, for how long?
- The amount of money the system is willing to invest. The assessment level should be in proportion to the risk (cost x likelihood) of failure and the overall value of the asset.
As the degree of inspection and amount of pipeline increases, the cost of the assessment increases.
When choosing direct assessment technologies pipe material is a major consideration. Well established in-pipe assessment tools are different for prestressed concrete cylinder pipe than they are for steel and ductile iron pipe, and tools for metallic pipelines are different than they are for PVC pipe. Since PVC doesn't corrode there is generally no need for tools to assess the pipe wall thickness. For larger systems with steel or ductile iron main transmission pipelines there are options using electromagnetic and ultrasonic technology that can provide an assessment of pipe wall thickness. A brief review of some tools for PVC, steel and ductile iron pipelines as discussed in M77 is summarized below.
Acoustic leak protection - The basic concept of finding leaks acoustically has not changed in many years. Leaks make noise and often can be heard with human ears. Because this method has been around for a long time and has been so successful more sophisticated options have been developed. Acoustic leak detection can be done externally as well as internal to the pipeline itself. How readily leaks are detected depends on the size of the leak, the size of the pipe, the pipe material, the distance between the leak and the detection device, and the background noise.
Listening devices can be placed on appurtenances that can be accessed above ground such as valves, hydrants and other fittings and the relative loudness gaged to localize or estimate the potential leak location but more sophisticated tools are required to pinpoint the leaks. Leak noise correlators can be used to analyze the acoustic signals received at two different external sensor locations to calculate a leak location to within several feet.
Internal acoustic devices get within inches of a leak which allows for precise location without the challenges of pipe material, diameter, and distances between listening points. Two primary types of in-pipe acoustic leak detection devices are available: tethered and free-swimming. Tethered devices are inserted at an access point and then propelled by the water flow past the leak which can then be located on the surface, usually within two feet. Tethered devices can be deployed up to 4,000 feet but can be limited by obstructions such as butterfly valves and multiple bends. Free-swimming devices are inserted at an access point and traverse the pipeline at a velocity proportional to the flowrate, recording acoustic data as they go. After the device is removed the data is downloaded and analyzed to determine whether leaks are present. Receivers can be installed on the exterior of the pipe to track the location of the device and increase the accuracy of leak location. The devices can record up to 20 hours of data for analysis which is the limitation of travel distance based on flow velocity. Some internal acoustic devices are as small at 2.5 inches in diameter allowing access to smaller distribution lines. Cost of internal acoustic device surveys is generally in the order of tens of thousand dollars per mile of pipe.
Electromagnetic Testing Technologies (EM) - EM technologies for pipe assessment can be used to determine changes in pipe wall thickness caused by corrosion, external damage, and depending on the equipment, cracking. These methods can be used externally for spot checks on the outside of the pipe with hand held tools or internally with various tools depending on the pipe size. The technologies all work by creating a magnetic field passing through the pipe wall and back to the tool. Variations in the pipe wall thickness as the tool moves along the pipe produce changes in the magnetic field which are detected and correlated to locations where corrosion or other pipe wall anomalies are present. Larger access points are generally needed for insertion and extraction of the internal devices than for acoustic testing devices. The tools vary in their inspection resolution with a general tradeoff between increased sensitivity and difficulty of pipeline access. Defects as small as ½ inch in size with 15 percent loss of wall thickness have been detected. The larger more sensitive tools require access points equivalent to the pipe diameter. Such access points typically do not exist in water distribution systems. Smaller, less sensitive tools can be inserted at smaller access points and can also navigate obstructions like bends and butterfly valves.
Ultrasonic Technology - Ultrasonic gauges are an advanced technique that can accurately measure depth of degradation and pipe wall thickness. An electrical pulse is converted into a high frequency ultrasonic sound wave which passes through the pipe material and reflects off the back wall and returns to the probe. Typically, these gauges have been used in external spot checks of un-lined steel pipe to determine the severity of internal corrosion and techniques are being developed for concrete and other cementitious pipe materials. New tools have recently been developed to take ultrasonic technology and mount it on in-pipe tools that can be inserted into the flow stream. These tools can be used in steel and ductile iron water pipelines with cement mortar linings to detect the presence and severity of external corrosion and do not require full pipe size access.
Costs for electromagnetic and ultrasonic in-pipe tools are an order of magnitude higher than those for acoustic in-pipe methods.
NEXT STEPS
Before starting a condition assessment, we recommend a review of the AWWA M77 manual to learn more about recommendations and considerations based on your specific system, budget and user needs.
At Bartlett & West we are tracking these and other technologies affecting water utilities. If you have any questions regarding the condition assessment information in this article, please don’t hesitate to contact us by using the form below.
Tell us about your project
We’d love to work with you. Tell us the services you are seeking and one of our team members will connect with you.